Our clients often ask us for Partnered Services and help in areas that is not our specialization, but we know the firms that can support and most often complement the work we do. Strategy Execution is what we specialize in, however if our clients need to evolve a business strategy we reach out to our partners. Similarly we support process improvements, but Product Engineering is what our partners can support. We also work with partners that provide training in Project Management
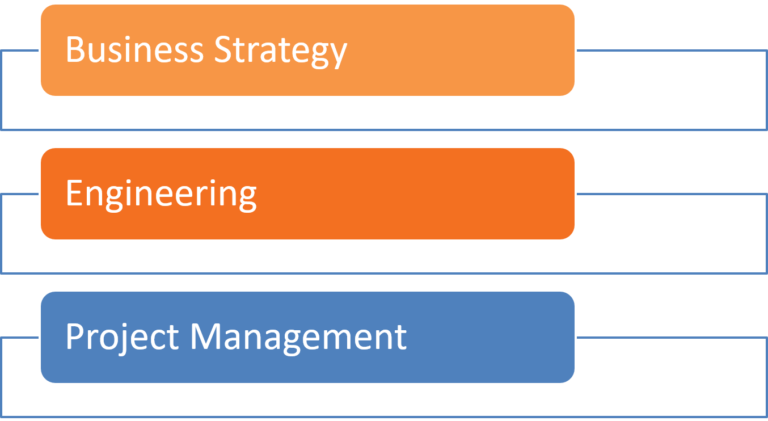